The carbon capture research area investigates the application of innovative CO2 capture technologies to the power and to the industry sectors (i.e., cement, steel, oil refinery). Most of the activities in the field focuses on the optimal integration within existing plants supported by specifically developed numerical models. Experimental activities related to the assessment of thermophysical properties of CO2 based mixtures are carried out at LEAP laboratory.
The GECOS group formulated the Specific Primary Energy Consumption per CO2 Avoided (SPECCA) coefficient which is widely adopted in the CCS sector to consistently compare different technologies.
Power sector
The power sector contributes for around 30% of the global CO2 emissions. Several technologies can contribute to mitigate the carbon intensity of the power sector. Innovative technologies are investigated to reduce the energy penalty as well as the additional costs related to the CO2 capture process. Examples of process investigated are:
Sorption Enhanced Water Gas Shift Membrane separation
Calcium-looping High temperature fuel cells
Sorption Enhanced reforming Mixed-Salt Technology
Chemical Looping Combustion Low Temperature Sorbents
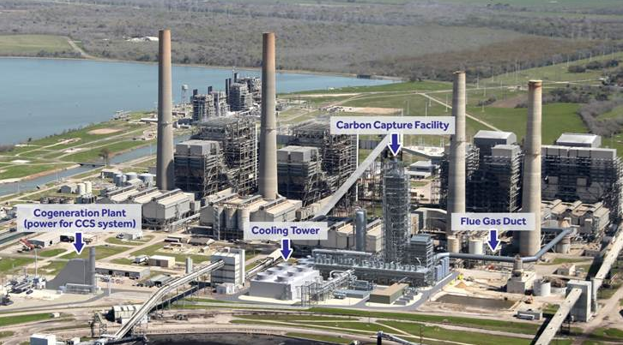
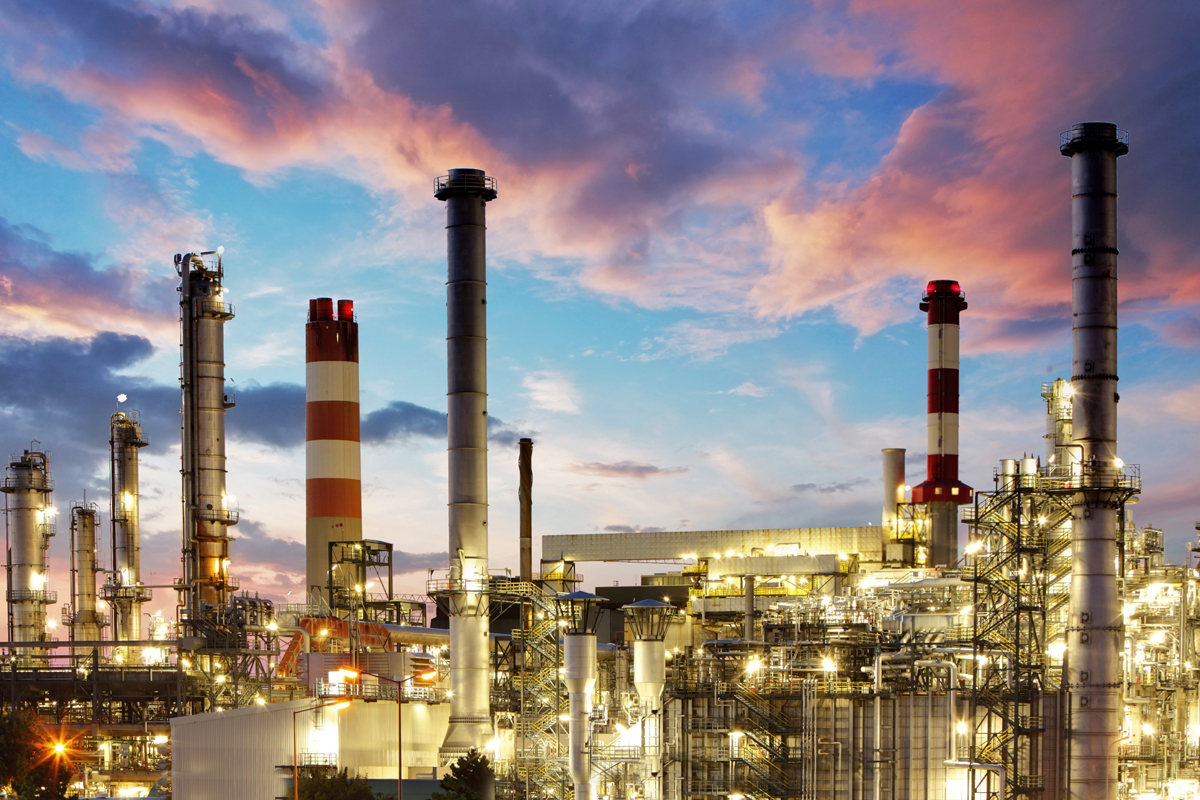
Industrial sector
Some industrial sectors are significant CO2 emitters which can contribute to some percent of the global CO2 emissions. Innovative process design integrating CO2 capture technologies are investigated to minimise the impact on the final product costs. Industrial sectors currently investigated are:
Cement
Integrated steel mills
Oil refineries and Steam Methane Reformers
Waste-to-Energy plants
Pulp and paper plants
Process optimisation
A strategy for reducing the CO2 emissions is the separation of CO2 from energy intensive processes and utilise it for chemical production. This concept relies on the wide diffusion of renewable non-dispatchable electricity generation which can be converted in hydrogen at limited costs. The hydrogen and CO2 reacts to produce chemicals as methanol. GECOS contributes to optimise the entire process from energetic and economic point of view.
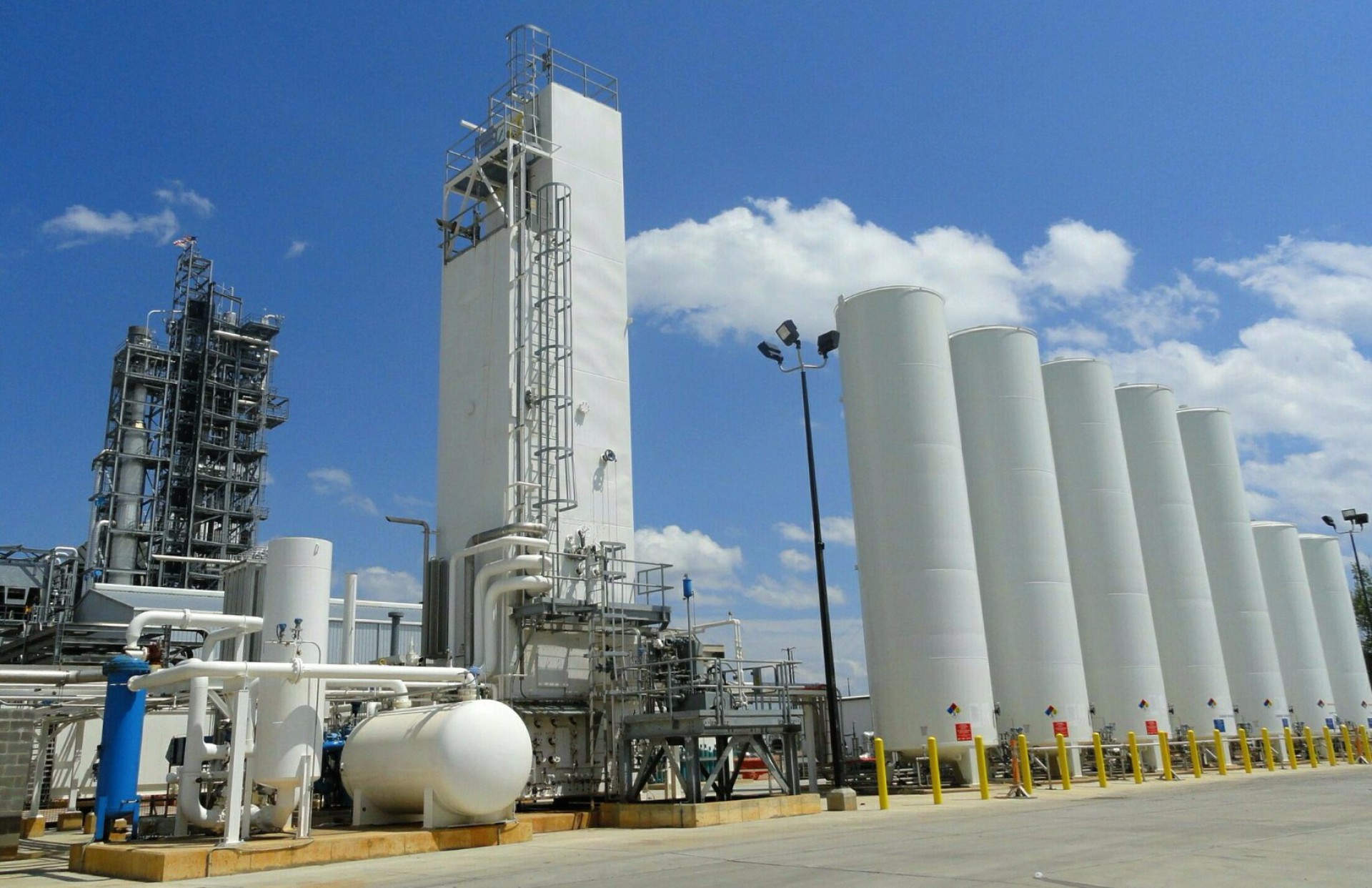
CO2 purification and compression
CO2 compression is one of the most energy intensive steps in the separation process. The energy consumption depends also on the CO2 purity and amount/type of contaminants. At LEAP laboratory an experimental activity regarding two-phase equilibrium and thermodynamic properties of CO2 rich mixtures is carried out.
For further information on carbon capture technologies, contact Prof. Matteo Romano at matteo.romano@polimi.it
Recent publications
Sorry, no publications matched your criteria.