Conventional steam Rankine cycles and open cycle gas turbines play a dominate role in large-scale power production. However there is a large variety of heat sources for which these option do not offer a technically and/or economically viable solution. In these cases the proper selection of the working fluid and of the cycle configuration allow to increase system efficiency, system flexibility and also to reduce the levelised cost of generated energy. Among these solutions the most studied within the GECOS group are the Organic Rankine Cycles (ORC) and the supercritical carbon dioxide cycles (sCO2).
ORC power systems
Organic Rankine Cycles adopt an organic compound (hydrocarbons, halogenated fluids, siloxanes) as working fluid. The possibility to select the main fluid properties allows to obtain large advantages in the design of the components and to always reach high conversion efficiency.
The challenge
The optimisation of an ORC system for a specific application is always a non-trivial task, because of the need to consider simultaneously:
the choice of the best working fluid
the selection and optimization of the best plant layout and components
the effects of fluid properties on expander efficiency
the influence of all these factors on the cost of the plant
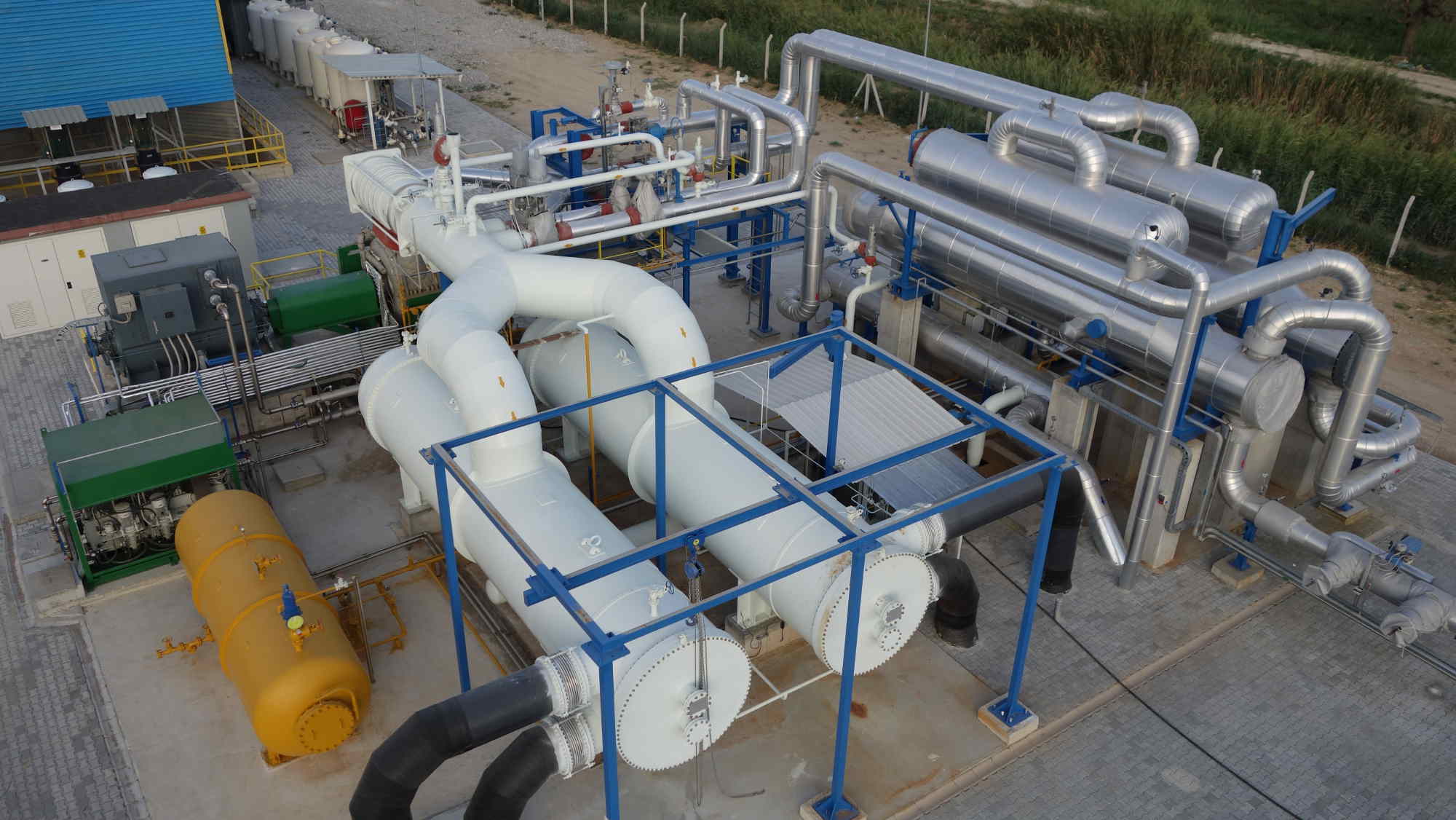
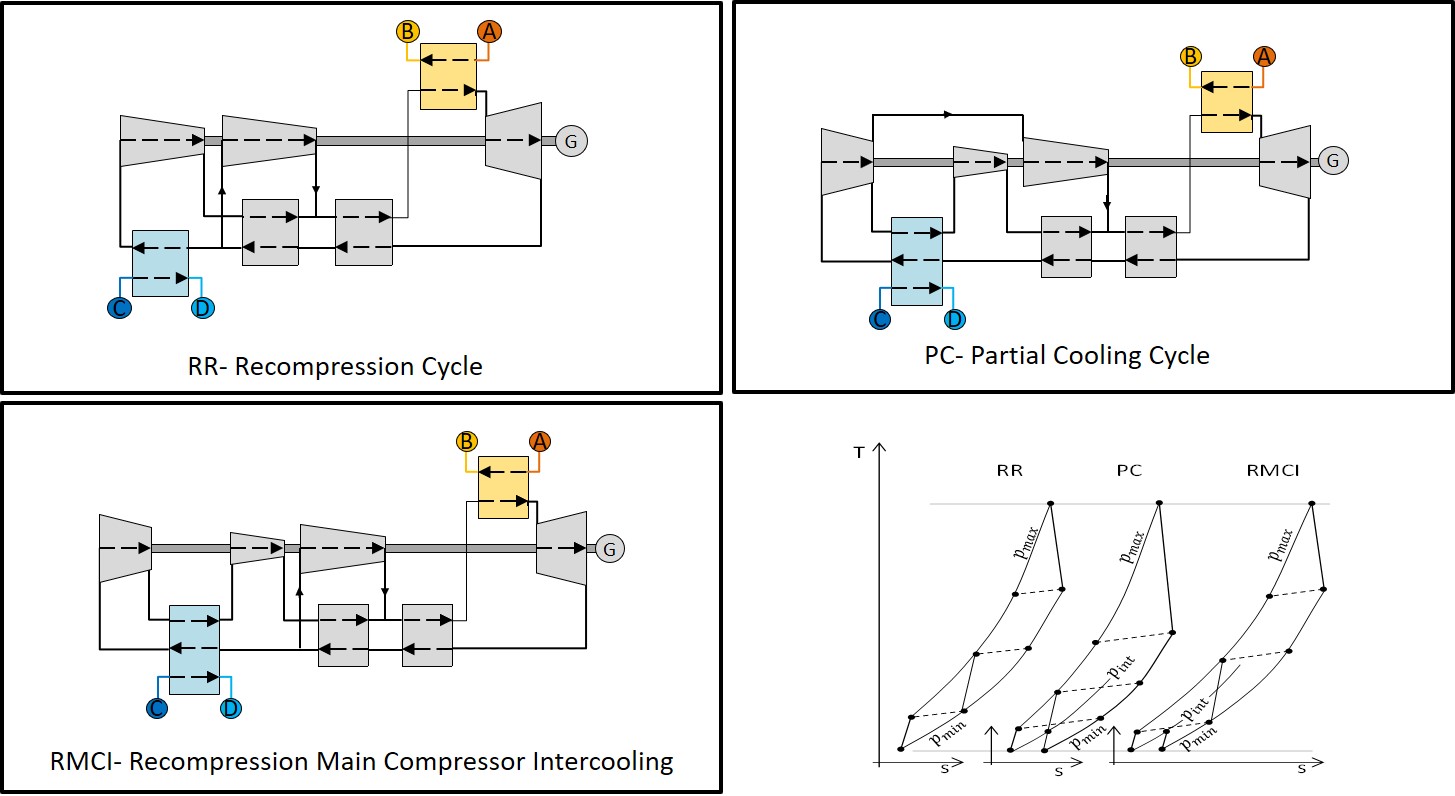
Supercritical CO2 power systems
sCO2 cycles can compete with steam Rankine cycles in high temperature applications thanks to the possibility to increase system efficiency and to increase flexibility. The concept is widely studied in literature but this technology is not commercial.
The challenge
The optimisation of these power plant is non-trivial task because of:
The large number (more than 40) of available cycle configurations differing in optimization criteria and strongly affecting the matching with the heat source
The presence of real gas effects at low temperature and high pressure that allow to reduce the compressor consumption but also requires reliable equation of state and a non conventional turbomachinery design
A challenging design of turbine stages and turbine shaft because of the very compact expander dimension and the high specific power
For further information, contact Prof. Marco Astolfi at marco.astolfi@polimi.it or Dr. Marco Binotti at marco.binotti@polimi.it
Related Projects
Recent publications
Sorry, no publications matched your criteria.